It’s well-known that once a product is built quality cannot be added into it. The work must be put in at the front end before the product is built. That means ensuring that the right material is being used, that procedures are well defined, and employees are well trained.
“You cannot inspect quality into a product.” Harold F. Dodge
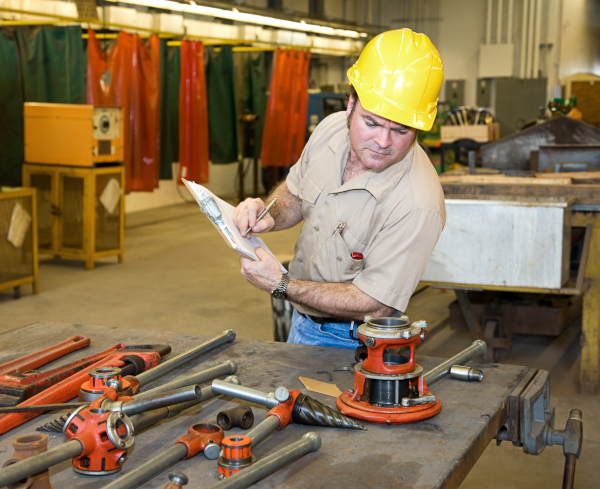
In this regard it might be helpful to understand the difference between two terms often used to ensure products meet the standard and quality specified by engineers and expected by customers.
Quality Control is “reactive” as it reviews the end-product to identify products that do not meet standards. An example of quality control is Statistical Process Control (SPC) whereby a random sample from each production run is analyzed for defective products. Again, once the product is built it’s too late to add more quality. You can pull items out of the process before it gets to the customer but obviously that is an expensive solution.
Quality Assurance is “proactive” as it monitors quality at every stage of the manufacturing process such as Quality at the Source (QATS). It catches and removes defects from the beginning to the end of every step. It encourages employee engagement in the quality process stopping further investment in a defective product.
Manufacturers must continually review their quality control and quality assurance measures to ensure their compliance with changes in production and meeting customer satisfaction.